문제 해결을 하려면 TRIZ에서 제공하는 기법과 개념을 몸에 익히기 위한 절차가 필요하다. TRIZ에서는 ARIZ가 가장 일반적인 프로세스로 사용되며 9단계를 거쳐 문제를 해결한다. 여기서는 ARIZ를 사용하지 않고 사례를 이용하여 문제를 풀어가는 과정을 경험해 본다.
하기 내용은 2001년 8월 일본 "Invetion User 모임"이라는 학회에서 발표된 내용으로 9월 Nikkei Mechanical 잡지에도 게재되었다. 레이저 다이오드(Laser Diode)는 레이저 빔을 만들어 내는 반도체 부품이다. 레이저 다이오드 개발 초기에는 '임계전류값'과 발진 시간이 가장 중요한 연구개발의 목표 값이었다.
임계전류값 : 레이저 다이오드에 전류를 공급하기 시작하면 일정 값에서부터 레이저 빛이 발생하기 시작하는데 이 전류의 값을 임계전류값이라고 한다.
임계전류값은 낮을수록 좋은데 발진 시간(수명)은 2만 시간 이상이어야 한다. 당시 개발 팀에서는 임계전류값의 평균이 200mA 정도였고 분산이 100mA였다. 그리고 발진 시간도 1.5시간이었다. 반면 업계 1위인 일본의 니치아 화학은 임계전류값 40mA에 수명이 1만 시간 이상이었다. 이럴 해결하기 위해 TRIZ가 융합된 6 Sigma가 진행되었다.
목표 정의(Define) 단계
프로젝트의 목표를 정확히 하기 위해 CTQ(Critical To Quality)를 확인해야 한다. 6 Sigma는 모든 일을 시작하기 전에 그 목적과 목표를 명확하게 한다. 연구개발에서는 그 목표가 연구개발의 목표와 일치될 수밖에 없다. 목표 정의(Define) 단계에서 임계전류값 50mA 이하 분산 10mA이하 그리고 발진 시간 1,000시간 이상으로 설정된 연구과제를 목표를 CTQ로 정하였다.
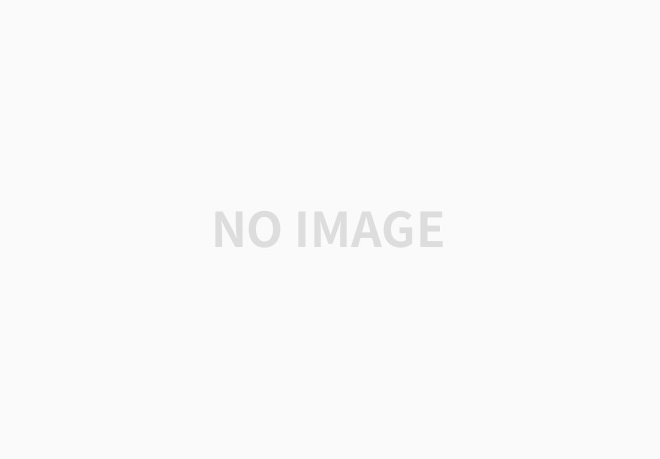
측정(Measure) 단계
6 Sigma에서 측정(Measure)단계란 "측정하지 않으면 개선 할 수 없다" 혹은 "측정되고 분석된 데이터가 문제의 해결책을 제시한다"라는 6Sigma 철학을 반영하는 단계이다. 하지만 수년 동안 최고의 인재들이 최고의 두뇌를 활용하여 최선을 다해 왔으므로 연구 데이터를 수집하고 분석한다고 해서 새로운 해결책이 나오는 경우는 없다. 해당 프로젝트 팀에서는 프로세스 매핑을 실시하여 목표 정의 단계에서 정한 목표를 달성하기 위해서 어떤 공정단계에서 개선이 이루어져야 하는지를 명확히 했다.
분석(Analyze) 단계
6 Sigma는 40, 50개가 넘는 Tool들의 집합체이다. 이 과제에서는 과연 어떤 Tool이 현재 봉착한 문제를 해결할 것인가를 고민하며 Tool들을 선택하였다. 아래와 같이 TRIZ와 실험계획법(DOE)만 사용하기로 했다.
Reducing Ith > Ridge Shape Change > TRIZ
Reducing the Varience of Ith > p-metal Process Change > TRIZ
Reducing the Varience of Ith > Optimization of Oxide Process > DOE
디자인(Design) 단계 : TRIZ 적용사례 1
레이저 다이오드 구조에서 상단의 릿지(Ridge) 부분의 구조가 성능에 가장 큰 영향을 미친다는 것을 배테랑 엔지니어는 경험으로부터 알고 있었다. 제작 공정에서 보호막(PR, Photo Resister)을 도포한 후 마스크를 이용하여 패턴을 만들고 식각(Etching)을 진행하여 릿지를 만들게 된다.
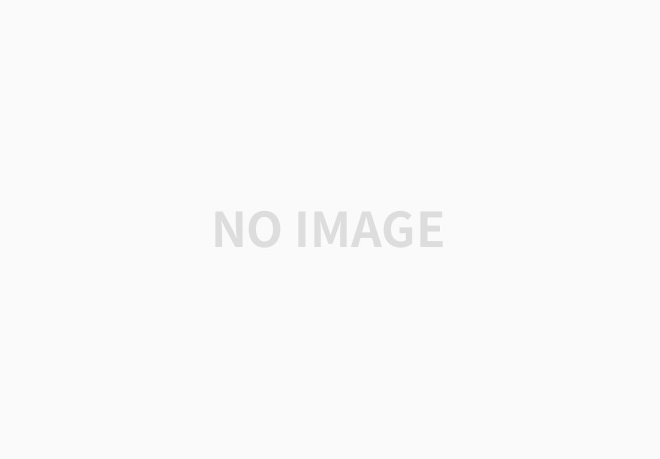
그런데 식각을 너무 적게 해서 얕게 깎아내면 전류 분산(Current Spreading) 현상이 일어나서 임계전류값이 상승한다. 또한 식각을 충분히 해서 릿지 부분을 깊게 깎아내면 전류 분산 현상은 일어나지 않는데 레이저 광이 발생했을 때 광 손실이 일어나 궁극적으로 임계전류값이 상승하게 된다.
"릿지 부분을 얕게 할 수도 없고 깊게 할 수도 없다."
이것은 물리적 모순이다. 곧바로 엔지니어는 분리의 법칙을 적용해 보았다. 시간에 의한 분리는 적용이 어려울 것으로 생각되었고 전체와 부분에 의한 분리도 어려울 것 같았다. 그래서 공간에 의한 분리를 적용하여 깊기도 하고 얕기도 해야겠다는 생각의 방향을 설정했다.
하지만 아무리 생각해도 이쪽 공간에서는 깊고 저쪽 공간에서는 얕게 한다는 것으로 해결책이 떠오르지 않았다. 고민을 계속하던 엔지니어는 식각(Etching) 공정에 의한 심리적 관성(Mental Inertia) 임을 인지하고, 공정에서 벗어나 왜 그런 구조를 가져야 하는지 고민하게 되었다.
우선 얕게 깎아 내면 전류가 옆으로 퍼지게 된다. 그리고 이것은 릿지 부분의 상단에서 일어나는 작용이다. 또한 깊이 깎아 내면 광 손실이 생기는데 이는 릿지 부분의 하단에서 발생하는 것이다. 그래서 엔지어는 상단과 하단을 분리하는 구조를 생각했고 자연스럽게 이온 경사 식각 방법을 고안하였다.
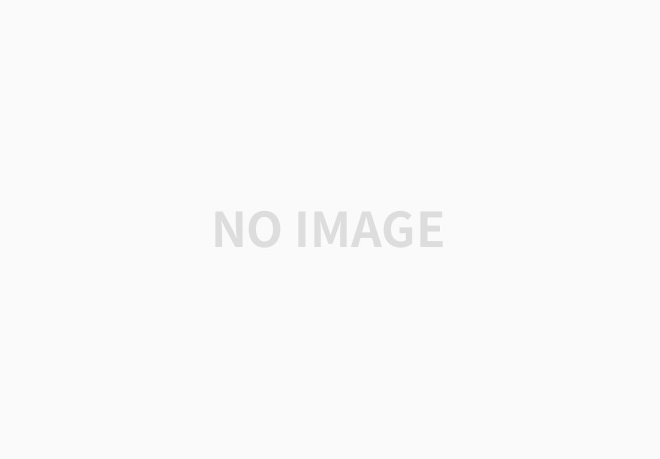
구조를 바꾼 후 임계전류값은 200mA에서 50mA로 획기적으로 감소했다. Breakthrough, 혁신이 일어난 것이다.
디자인(Design) 단계 : TRIZ 적용사례 2
릿지부의 상단에는 p-금속이 놓이는데 이것은 전극의 기능도하지만 다이오드 소자 내부에서 발생한 열을 열전도를 통해 외부로 배출하는 기농도 있다. 아래와 같은 공정단계에서 p-금속을 생성시킬 장소를 마련하기 위한 접촉홈생성공정(Contact Hole Process)이 있는데 접촉홈의 폭이 1.5um이기에 정확히 릿지부 상단에 일치시키기가 어렵다. 이런 정밀도를 요하는 공정 때문에 임계전류값의 분산이 100mA 이상이 되는 것이다.
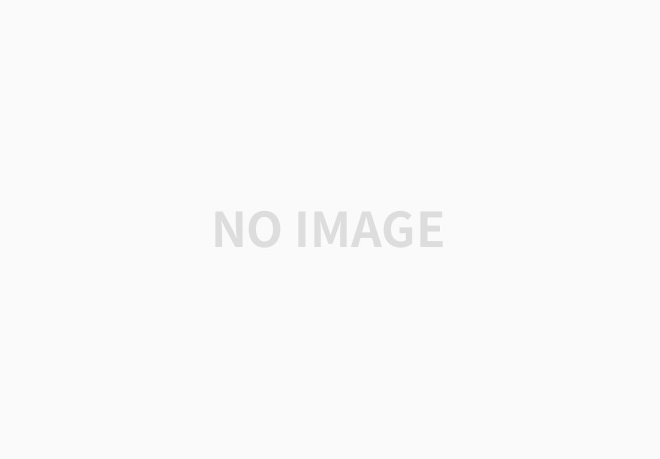
해당 팀에서는 분산의 문제는 제외하고, p-금속의 폭을 늘려서 소자의 작동시간을 증가시키려고 하였다. 열을 외부로 용이하게 전달하기 위함이었다. 그런데 p-금속의 폭을 증가시켜 소자의 작동시간을 늘릴 수 있었지만 p-금속을 통한 전류의 손실이 발생하였다. 엔지니어는 이를 기술적 모순으로 인식하였다.
여러 번의 시행착오 끝에 좋아지는 변수를 '정지해 있는 물체의 길이', 나빠지는 변수를 '에너지 손실'로 정의하였다. 모순 테이블에 적용하여 6번(범용성/다양성)과 26번(복제)의 원리를 적용해보려 했지만 TRIZ가 익숙하지 않아서 원리를 적용하지 못하였고, 적용 예제 중에서 자동위치 교정 공정(Self Alignment Process)을 발견하였다.
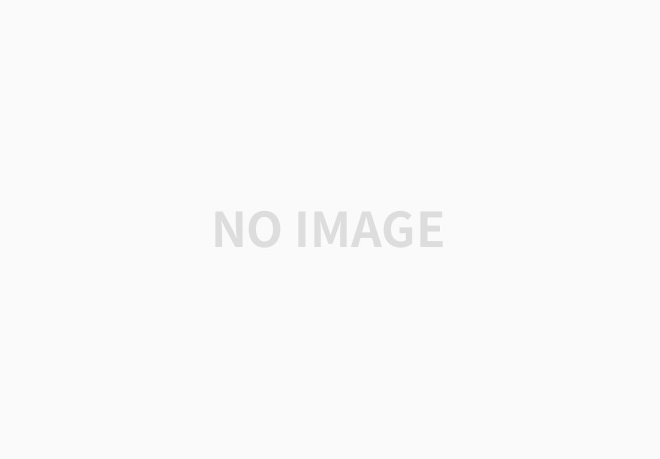
예전 공정에서는 릿지부 형성을 위한 보호 마스크를 릿지부 형상 후 완전히 제거하고 다시 그 위에 절연막을 쌓았다. 그 후 다시 절연막의 중심부분을 1.5um로 제거하는 접촉홈생성공정을 거쳐야했다. 개선된 공정은 릿지부 형성 시에 사용했던 보호 마스크를 제거하지 않고 그 위에 곧바로 절연막을 입힌 후 그때서야 보호 마스크를 제거하여 자동으로 1.5um부분을 확보할 수 있었다. 6번 원리 "한 부품을 여러 번, 여러 용도로 사용하기"가 적용된 것이다.
디자인(Design) 단계 : DOE
물리적 모순을 해결하여 릿지부의 모양을 경사지게 하였는데 어떤 각도가 최적일까? 릿지의 폭은 얼마가 되어야 할까? 5 ~ 6가지의 변수를 동시에 조정하려면 실험계획법을 통해서 알아내는 것이 가장 현명하다. 최적화에 있어 실험계획법이 가장 강력한 방법론이다.
검증(Verify) 단계
물리적 모순을 해결하여 평균값을 이동하고 기술적 모순을 해결하여 산포를 줄였다. TRIZ를 통한 아이디어는 DOE를 통해서 그 효과가 극대화되었다. 검증 단계에서는 반복 실험을 통해 그 결과가 검증되었다.
도서 : "생각의 창의성" , 김효준 지음 인용.
'TRIZ > 일반 이론' 카테고리의 다른 글
[TRIZ] 좋은 답과 TRIZ의 핵심개념 (0) | 2021.05.17 |
---|---|
[TRIZ] 좋은 해결책의 일반적 특징 (0) | 2021.05.17 |
[TRIZ] 40가지 원리와 39가지 기술적 표준용어(기술모순매트릭스) (0) | 2021.05.17 |
[TRIZ] 모순(Contradiction) (0) | 2021.05.17 |
[TRIZ] 트리즈 소개 (0) | 2021.05.17 |